Just How Plastic Nameplates Are Made: A Comprehensive Overview to Their Manufacturing Process
The manufacturing of plastic nameplates entails a number of specific actions, starting from the option of ideal materials to the final complements. Each stage is essential, making certain the item fulfills certain demands for longevity and appearances. Numerous manufacturing methods play a substantial role in crafting these nameplates. Recognizing these procedures can shed light on the complexities behind what might look like an easy product. What elements contribute to the quality and modification of these nameplates?
Comprehending Plastic Materials Used for Nameplates

The Design Refine: From Principle to Prototype
The style procedure for plastic nameplates starts with a clear concept that guides the total development. Developers work together with customers to specify the objective, design, and details demands of the nameplate. This first stage includes conceptualizing sessions, laying out ideas, and choosing colors and typefaces that line up with branding goals.Once the principle is developed, developers utilize computer-aided style (CAD) software program to create in-depth digital depictions. These models permit visualization and adjustments before moving on. Feedback from stakeholders is important throughout this stage, as it assists fine-tune the style to fulfill expectations.After completing the digital model, a physical design might be generated, usually through techniques like 3D printing. This tangible representation allows more examination of aesthetics and capability. On the whole, the style procedure is a crucial action that lays the foundation for the reliable production of premium plastic nameplates.
Cutting and Forming the Plastic
In the cutting and forming phase of plastic nameplate manufacturing, the choice of products plays a crucial role in figuring out the final item's quality and resilience (Plastic Nameplates). Numerous precision cutting strategies, such as laser cutting and CNC machining, warranty that the plastic is formed with precision and uniformity. This mix of cautious material selection and progressed cutting approaches is crucial for generating high-grade nameplates
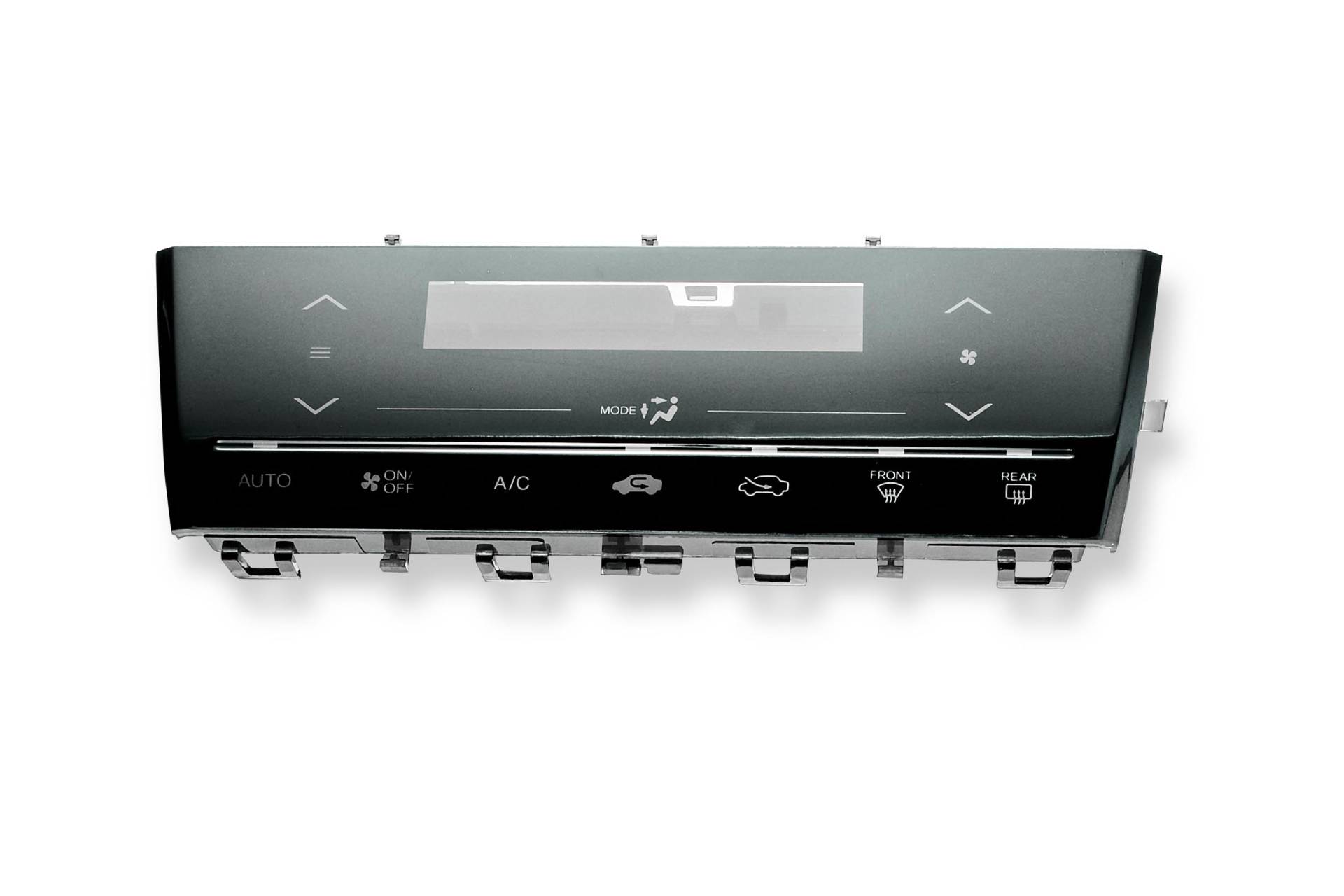
Product Choice Process
Selecting the ideal product is crucial for creating high-quality plastic nameplates. Various sorts of plastics are readily available, each offering unique advantages and qualities. Common options consist of acrylic, polycarbonate, and PVC. Acrylic is preferred for its clearness and UV resistance, making it perfect for exterior applications. Polycarbonate, known for its durability and effect resistance, is suitable for environments that call for boosted defense. PVC is frequently picked for its cost-effectiveness and versatility in design. The selection process additionally takes into consideration factors such as color, surface area, and density finish, which can substantially affect the final look and capability of the nameplate. Inevitably, the chosen material must line up with the meant use and visual goals of the plastic nameplate.
Precision Cutting Methods
While choosing the appropriate product lays the groundwork, accuracy reducing strategies play an important duty fit the plastic nameplates right into their last forms. Various approaches, consisting of laser cutting, CNC milling, and pass away reducing, are used to accomplish accuracy and uniformity. Laser cutting uses focused light to produce detailed layouts and clean sides, suitable for complicated patterns. CNC milling provides flexibility by removing excess material with accuracy, accommodating numerous densities and forms. Die cutting, on the other hand, allows for mass production of consistent pieces, enhancing efficiency. Each technique is picked based upon the design specs and the preferred finish, making certain that the last item fulfills high quality requirements and customer assumptions while maintaining durability and aesthetic allure.
Printing Techniques for Modification
Just how can makers accomplish accurate and vibrant layouts on plastic nameplates? The response hinges on various printing techniques tailored for personalization. Digital printing has actually obtained popularity because of its ability to generate high-resolution pictures and detailed designs straight onto plastic surfaces. This technique permits fast turnaround times and very little setup costs, making it optimal for brief runs and personalized orders.Screen printing continues to be another extensively made use of method, especially for bigger amounts. It entails producing a why not look here stencil and using layers of ink, leading to rich colors and resilience. UV printing, which uses ultraviolet light to heal the ink, is also efficient, offering excellent adhesion and resistance to fading.Additionally, pad printing uses convenience for irregularly shaped nameplates, enabling for thorough styles on challenging surfaces. These printing methods allow suppliers to satisfy varied client requires while ensuring quality and longevity in their plastic nameplate items.
Surface Area Treatments and Finishing Options

Quality Assurance Measures in Manufacturing
Guaranteeing the greatest standards of quality assurance during the production of plastic nameplates is important for keeping item honesty and client complete satisfaction. Producers execute extensive inspection protocols at various phases of the production process. Raw products undergo complete screening to verify they satisfy specs for longevity and shade consistency. Throughout the molding phase, automated systems keep track of specifications such as temperature level and stress to avoid defects.In addition, aesthetic evaluations are conducted to identify any kind of surface blemishes or imbalances. When the nameplates are produced, they go through practical examinations, including attachment examinations for printed components and cardiovascular test explanation for resilience. Quality assurance groups often use analytical tasting techniques to analyze sets, ensuring that any deviations from requirements are promptly resolved. This comprehensive technique not only improves item top quality however additionally fosters depend on with customers, verifying the supplier's dedication to quality in every nameplate created.
Product packaging and Circulation of Finished Nameplates
The product packaging and circulation of ended up plastic nameplates are important action in ensuring they reach clients in perfect problem. Different product packaging materials are selected to protect the nameplates during transit, while shipping approaches are carefully selected based on effectiveness and cost-effectiveness. Furthermore, reliable storage space solutions are applied to preserve top quality until the nameplates are provided.
Product Packaging Materials Utilized
Choosing proper packaging products is essential to guarantee their security during transportation when distributing finished plastic nameplates. Commonly used products consist of bubble cover, foam extra padding, and cardboard boxes, all developed to support the nameplates versus influences and shocks. Bubble cover offers an adaptable barrier, while foam extra padding warranties that nameplates stay safely in area, decreasing the threat of scratches or breakage. Additionally, sturdy cardboard boxes are utilized to consist of the nameplates, offering architectural assistance and protection from external components. Tags may be related to suggest dealing with directions or fragile components, further improving safety and security during transport. Generally, making use of top notch product packaging products substantially adds to the integrity and presentation of the finished plastic nameplates upon arrival at their destination.
Shipping Approaches Employed
Efficient distribution of ended up plastic nameplates relies on various shipping methods that guarantee timely and safe shipment. Firms frequently utilize copyright solutions, products delivery, and postal services, depending upon the dimension, weight, and location of the packages. For regional distributions, messenger solutions provide rapid transportation, guaranteeing nameplates reach customers quickly. For larger orders, freight shipping is preferred, utilizing trucks or shipping containers to move bulk amounts efficiently. Post offices offer as an economical choice for smaller sized deliveries, especially for domestic deliveries. All shipping methods focus on safety product packaging to protect against damages throughout transportation. Tracking systems are likewise used to keep an eye on deliveries, supplying clients with real-time updates and confidence concerning the condition of their orders.
Storage Solutions Implemented

Often Asked Concerns
What Sorts Of Businesses Commonly Utilize Plastic Nameplates?
Plastic nameplates are generally utilized by various businesses, consisting of offices, health centers, institutions, and manufacturing facilities. These nameplates serve crucial functions such as recognition, info display screen, and branding, adding to organizational efficiency and expert look throughout varied settings.
For how long Does the Entire Manufacturing Process Take?
The production process duration varies based upon intricacy and amount, generally ranging from a couple of days to several weeks. Variables influencing this timeline include design authorization, product accessibility, and manufacturing strategies used by the firm.
Can Plastic Nameplates Be Recycled After Usage?
Plastic nameplates can be recycled, Get the facts offered they are made from recyclable products. The availability of reusing programs and neighborhood policies might affect their recyclability. Correct disposal practices are vital to ensure reliable recycling.
What Are the Ecological Effects of Plastic Nameplate Production?
The environmental effects of plastic nameplate production consist of carbon emissions, resource depletion, and contamination from making procedures. Plastic Nameplates. Furthermore, incorrect disposal adds to plastic waste, negatively affecting ecosystems and wild animals, highlighting the requirement for sustainable practices
Exist Any Type Of Safety And Security Issues With Plastic Nameplates?
Safety and security problems concerning plastic nameplates mainly entail potential chemical exposure throughout production and the risk of products breaking down in time, which may result in unsafe compounds being launched, affecting both human health and wellness and the setting. While various materials can be used for nameplates, plastic remains a popular selection due to its convenience and resilience. In the cutting and forming phase of plastic nameplate production, the choice of products plays an important duty in figuring out the final product's quality and sturdiness. Choosing the appropriate material is crucial for creating high-quality plastic nameplates. While picking the proper material lays the foundation, precision reducing techniques play a vital role in shaping the plastic nameplates right into their final kinds. When dispersing completed plastic nameplates, choosing appropriate product packaging materials is vital to guarantee their security throughout transportation.